Vendor Managed Programs
Toolneeds offers complete Vendor Managed Programs to help take the pressure off your staff when sourcing and purchasing commonly used MRO consumables, PPE and tooling products. Our VMI Specialists will become an extension of your staff. They will track, source, order and deliver in the products that you need. These products will then be put into our vending systems to allow your employees to issue the items they need quickly and efficiently.
Vendor Management
& Industrial Vending
Toolneeds utilizes these systems in our VMI programs to help you realize significant control and savings with your consumable. Utilizing AutoCrib® systems you can save millions of dollars..
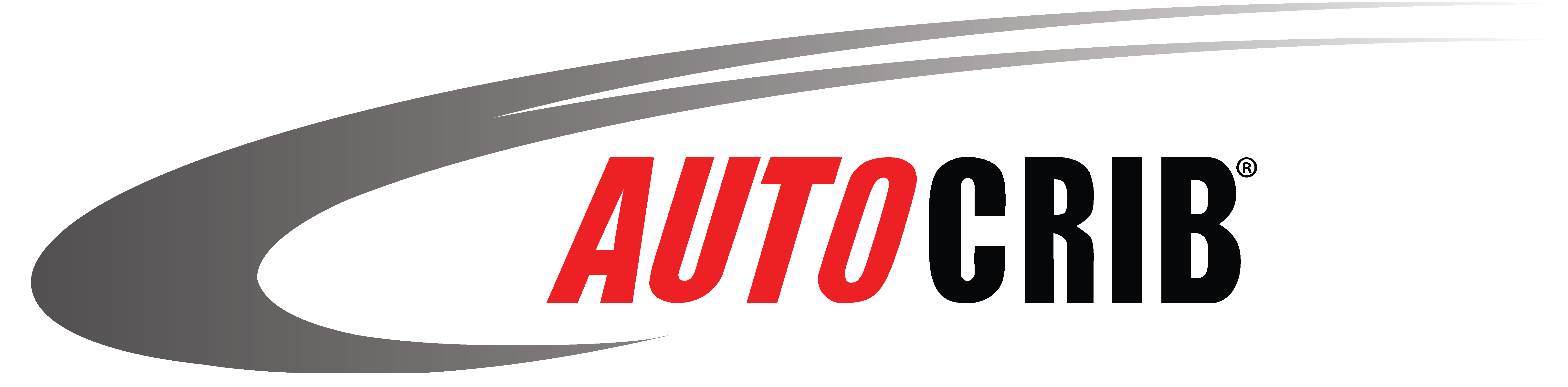
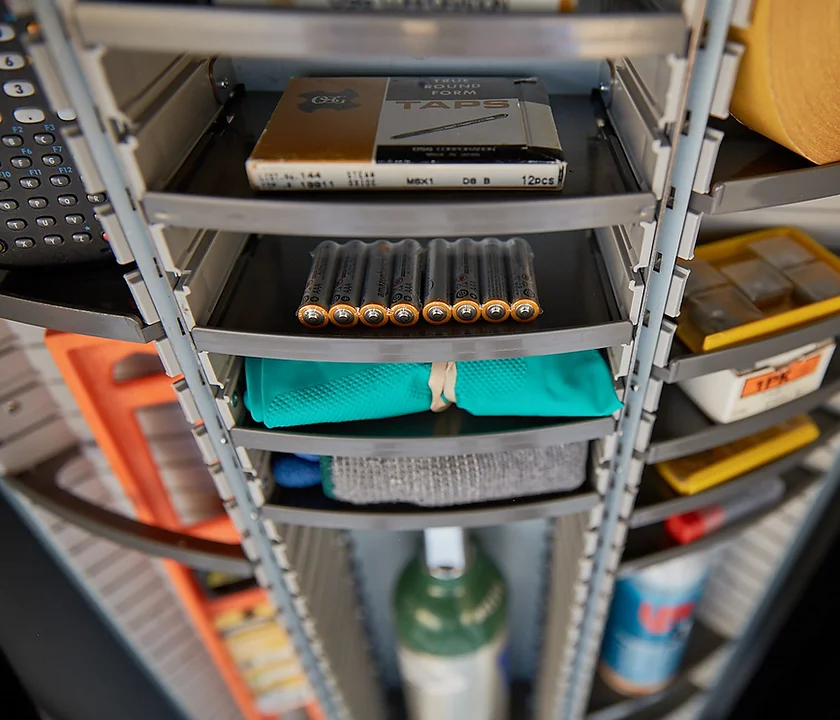
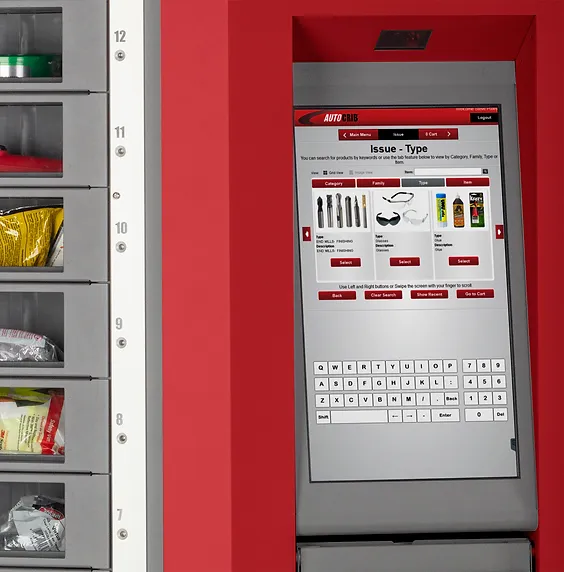
8 WAYS TO REDUCE COST
Vendor managed programs made easy
-
Inventory Management
Good Inventory Management practices can help your company plan, control and organize the goods and materials required for your business's day to day operations. Toolneeds utilizes the Industry leading Inventory Management software and Vending systems from AutoCrib.
ORGANIZE — REDUCE SPEND — TRACK USAGE — SAVE TIME
-
AutoCrib Software
Our industrial vending systems are driven by AutoCrib®'s powerful software, which gives you real-time usage data and in many cases, will update your ERP system. This helps you dramatically reduce the cost of indirect supplies by as much as 20-40% –– Your employees are now accountable, and you control access to tools and supplies.
POWERFUL — SIMPLE — CONTROL — MOBILE
-
Vending Systems
To date, AutoCrib® has over 20,000+ industrial vending systems installed in 40+ countries that include the US, Canada, Mexico, Australia, Europe, South America, Middle East, and Asia.
ACCURATE — SECURE — FAST — AUTOMATED
Take the first step
The first thing we do is schedule an assessment of the current situation at your facility. Once completed we can make suggestions on how a VMI program would help. From making sure the products are kept in secure but accessible location to reducing your current inventory to a level that allows for continued production without over stocking, we will make sure to get your facility as lean as possible.